泓川科技光谱共焦传感技术:AR眼镜制造中测量镜片间隙的"微米级裁判"
在AR眼镜的光学系统中,镜片层间若存在2微米的装配误差,足以让虚拟影像产生肉眼可见的错位。这种堪比微雕艺术的精密组装需求,正推动光谱共焦测量技术从实验室走向智能制造前线,成为保障光学性能的"质量守门员"。
当透明遇上透明:层间测量的光学迷宫
AR镜片的层叠结构犹如透明千层酥:
- 间隙控制红线:行业标准要求5-80μm(约蝉翼厚度的1/5至2倍)
- 传统检测的三大痛点:
√ 接触式测量:0.6N测力可导致超薄玻璃0.8μm弯曲变形
√ 激光反射法:多层反射信号相互干扰形成"鬼影"数据
√ 离线抽检:无法捕捉动态组装过程的瞬时波动
波长解构的测量革命
这项技术通过光学"色谱尺"实现层间解密:
- 色散编码:白光经特殊透镜分散形成轴向色差,每个波长对应特定焦点深度
- 光谱解析:接收端光栅将反射信号分解为"光学指纹"图谱
- 智能运算:基于MEMS微镜的高速扫描实现50nm级坐标定位
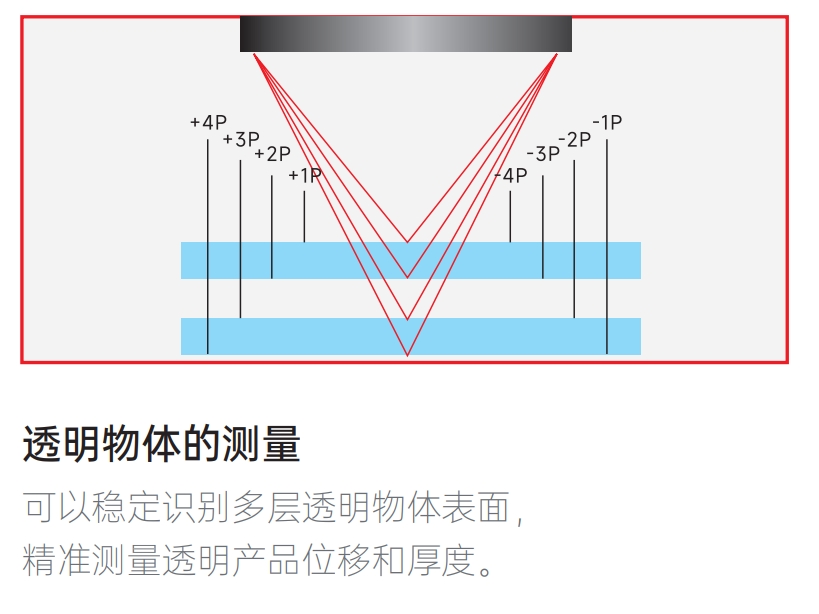
以LTC2600系列工业传感器为例的性能表现:
- 穿透能力:单次测量可识别4层玻璃8个界面
- 精度体系:
▶ 绝对精度:±0.3μm(相当于蜘蛛丝直径的1/3)
▶ 温度漂移:<1nm/℃(优于石英玻璃膨胀系数)
- 场景适配:
Φ9μm针尖光斑——检测高反光金属镀膜边界
Φ144μm漫射光斑——应对雾化防眩涂层的散射挑战
智能工厂的精度革命
某月产20万套AR镜片的智能产线改造案例:
- 在线检测系统架构:
- 16通道控制器同步处理多工位数据
- 10kHz采样率捕捉注胶固化过程形变
- 过程能力对比:
指标 | 改造前 | 改造后 | 提升幅度 |
---|---|---|---|
CPK值 | 0.82 | 1.58 | 92.7% |
单件检测耗时 | 38秒 | 0.4秒 | 99% |
年返工成本 | ¥260万 | ¥17万 | 93.5% |
技术落地的三维适配
图示:不同生产场景的技术配置方案
实施策略建议:
- 研发阶段:LTC2600+六自由度微调平台(定位精度0.1μm)
- 量产阶段:多传感器阵列+机器视觉引导(UPH提升300%)
- 特殊工艺:高温版传感器+真空吸附夹具(耐温200℃)
技术延伸的产业浪潮
这项测量技术正在引发光学制造的范式转移:
- 工艺创新:支持0.01°级倾角调节的主动对准系统
- 材料革命:推动0.3mm超薄微晶玻璃量产应用
- 数字转型:通过C#SDK实现SPC数据直通MES系统
正如行业专家所言:"过去我们像在雾中调整镜片间隙,现在光谱共焦技术拨开了这层迷雾。"这项融合了光学、算法和精密机械的测量方案,不仅重新定义了AR眼镜的制造标准,更开启了透明介质精密测量的全新时代。